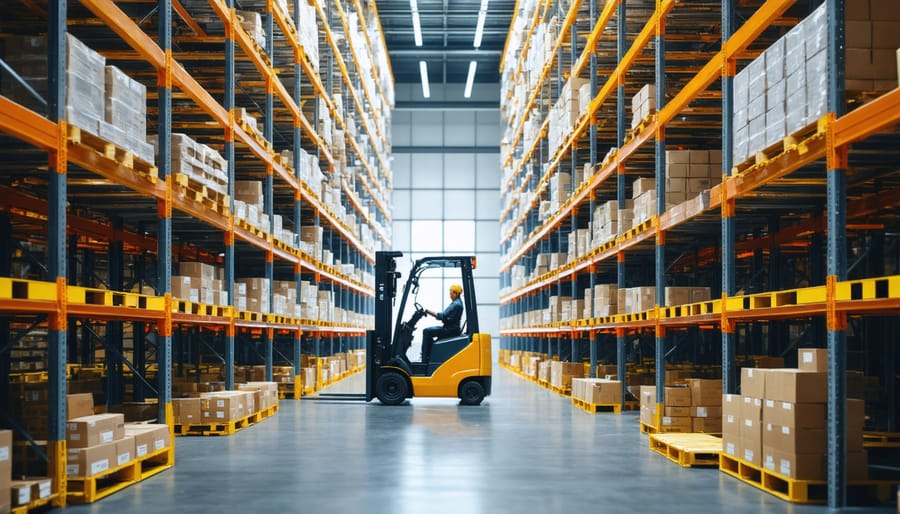
Smart Storage Solutions That Transform Your Warehouse Space
Transform your warehouse operations by implementing vertical storage systems that maximize every square foot from floor to ceiling. Strategic aisle configuration, integrated with modern warehouse management software, creates efficient picking paths while reducing wasted space by up to 40%. Automated storage and retrieval systems (AS/RS) revolutionize space utilization through high-density storage solutions, enabling 85% more inventory capacity compared to traditional racking methods. Zone-based organization, coupled with real-time inventory tracking, optimizes product placement based on movement frequency and seasonal demands. These data-driven approaches not only enhance storage density but also improve order fulfillment speed and accuracy while maintaining safe, accessible workspaces for warehouse staff.
Vertical Space Maximization Strategies
High-Rise Shelving Systems
High-rise shelving systems represent one of the most effective approaches to vertical space utilization in modern warehouses. These systems typically extend from floor to ceiling, offering multiple levels of storage that can dramatically increase your warehouse’s storage capacity without expanding its footprint.
Popular options include selective rack systems, which provide direct access to all storage locations, and drive-in racks that maximize density by eliminating aisles between rows. For smaller operations, adjustable steel shelving units offer flexibility and easy reconfiguration as needs change.
The benefits of high-rise shelving extend beyond just increased storage capacity. These systems can improve inventory organization, speed up picking operations, and enhance workplace safety when properly implemented with appropriate access equipment like forklifts or order pickers.
When selecting a high-rise system, consider factors such as:
– Product dimensions and weight
– Access frequency requirements
– Available ceiling height
– Floor load capacity
– Equipment compatibility
Modern high-rise systems can be integrated with warehouse management software and automated picking systems, making them an excellent foundation for future technological upgrades. They’re particularly effective when combined with proper aisle planning and inventory management strategies, creating an efficient and organized storage solution that grows with your business.
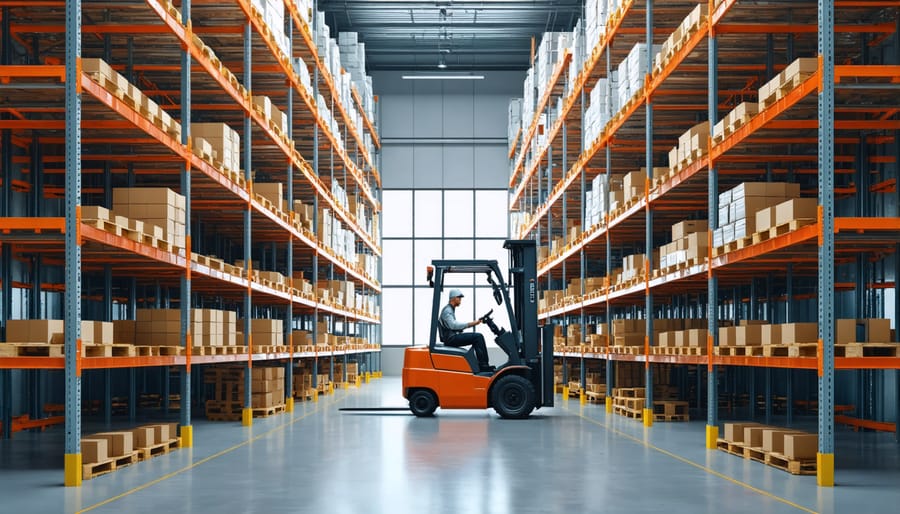
Mezzanine Installation Benefits
Mezzanine installations offer a game-changing solution for warehouses struggling with limited floor space. By creating an additional level within your existing warehouse structure, you can effectively double your storage capacity without expanding your building’s footprint. These elevated platforms are particularly valuable for storing lighter inventory, office equipment, or creating dedicated picking areas.
Installing a mezzanine floor brings multiple benefits beyond just increased storage space. The additional level can be customized to accommodate various needs, from bulk storage to creating climate-controlled areas for sensitive items. Many businesses use mezzanine spaces for organizing smaller items or establishing efficient picking stations, improving overall workflow efficiency.
The beauty of mezzanine installations lies in their versatility. You can opt for different flooring materials, ranging from steel grating to solid panels, depending on your specific requirements. Adding features like safety railings, staircases, and freight elevators ensures safe and convenient access to the upper level. For enhanced efficiency, consider incorporating conveyor systems or pallet gates to streamline material movement between levels.
One often-overlooked advantage is the cost-effectiveness of mezzanine installations compared to facility expansion or relocation. The installation process is relatively quick, causing minimal disruption to your daily operations. Plus, mezzanine structures can be disassembled and relocated if needed, offering flexibility for future warehouse modifications.
Smart Zoning and Layout Planning
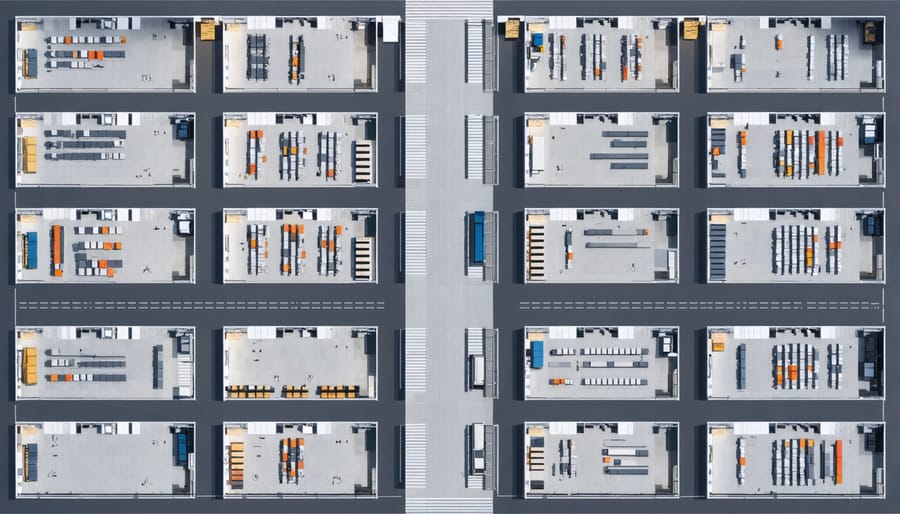
Flow Pattern Optimization
Efficient flow patterns are the lifeblood of a well-organized warehouse, directly impacting productivity and worker satisfaction. Start by mapping out your current movement patterns – observe how staff, equipment, and materials travel through your space during typical operations. Look for bottlenecks, unnecessary zigzagging, or areas where traffic frequently crosses paths.
Consider implementing a one-way flow system where possible, creating dedicated lanes for different types of movement. Popular patterns include U-shaped flows, where receiving and shipping are on the same side, and straight-line flows, which work well in rectangular spaces. Place frequently accessed items near main thoroughfares and group related products together to minimize travel time.
Zone your warehouse strategically by creating designated areas for specific activities: receiving, picking, packing, and shipping. This natural workflow progression reduces confusion and prevents congestion. Don’t forget to factor in seasonal changes – ensure your flow patterns can adapt to busy periods without creating chaos.
Leave adequate aisle width for equipment maneuverability while maximizing storage density. A good rule of thumb is to make main aisles wider than secondary ones, typically 12-13 feet for main thoroughfares and 8-10 feet for picking aisles. Consider using mobile storage solutions in less frequently accessed areas to create flexible pathways that can be opened when needed.
Mark your flow patterns clearly with floor tape, signs, and directional arrows. This visual management approach helps new staff adapt quickly and maintains orderly movement throughout your facility. Regular review and adjustment of these patterns ensure they continue to serve your operation’s evolving needs.
Activity-Based Storage Areas
One of the most effective ways to optimize warehouse space is by organizing storage areas based on how frequently items are accessed. This approach, often called “ABC analysis” or “velocity-based storage,” can significantly reduce picking times and improve overall efficiency.
Start by analyzing your inventory movement patterns and categorizing items into three main groups: high-frequency (A items), medium-frequency (B items), and low-frequency (C items). High-frequency items should be placed in easily accessible areas near picking and packing stations, ideally at waist height to minimize bending and reaching. These “golden zones” make daily operations smoother and reduce worker fatigue.
Medium-frequency items can occupy the middle ground, placed in areas that require minimal travel time but don’t need prime real estate. Consider using mid-level rack positions or secondary aisles for these products. Low-frequency items, such as seasonal products or slow-moving inventory, can be stored in less accessible areas, higher rack positions, or even in separate storage zones.
Remember to regularly review and adjust your storage layout as item popularity changes. What’s hot today might not be tomorrow, so maintain flexibility in your storage system. Using mobile shelving units or modular racking systems can make it easier to adapt your layout as needed.
Pro tip: Create clear zone markers and use color-coding to help workers quickly identify different storage areas. This visual management system can dramatically improve picking accuracy and speed while reducing training time for new staff.
Technology Integration for Space Efficiency
Automated Storage Systems
Modern warehouses are embracing automated storage and retrieval systems (AS/RS) as one of the most efficient storage solutions available today. These smart systems use robotic technology to store and retrieve items automatically, dramatically reducing the need for manual handling while maximizing vertical space usage.
The heart of an AS/RS typically consists of computer-controlled cranes that move along aisles between storage racks, placing and picking items as needed. These systems can reach heights of up to 100 feet, making full use of vertical space that would be impractical to access with traditional methods. The computer tracks every item’s location, ensuring accurate inventory management and faster retrieval times.
Popular AS/RS options include shuttle systems for smaller items, mini-load systems for medium-sized products, and unit-load systems for palletized goods. Each type can be customized to fit specific warehouse needs and product types. The benefits are substantial: reduced labor costs, improved accuracy, faster operation speeds, and better space utilization.
While the initial investment may be significant, businesses typically see returns through increased efficiency, reduced errors, and better use of available space. For warehouses dealing with high-volume operations or limited floor space, automated storage systems can be a game-changing solution.
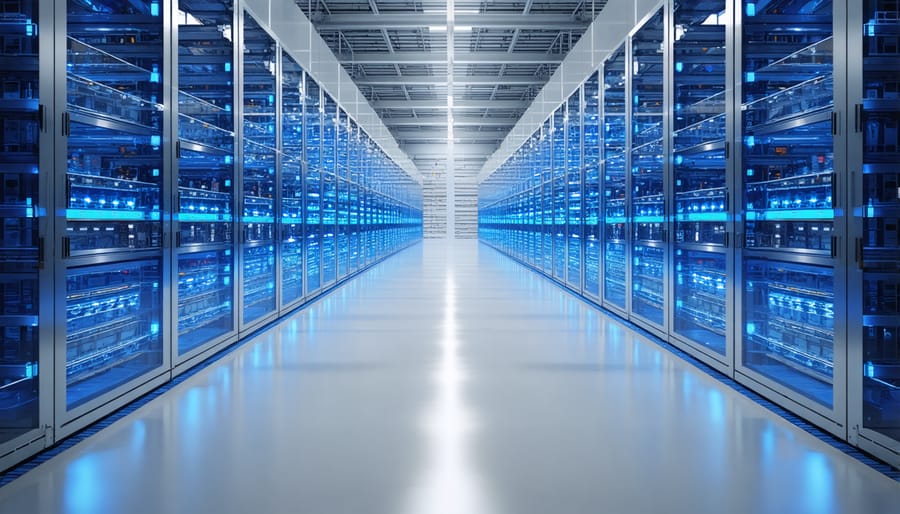
Inventory Management Software
Modern inventory management software has revolutionized how warehouses track and optimize their space usage. These smart solutions offer real-time visibility into your storage areas, helping you make data-driven decisions about space allocation and product placement.
With advanced tracking features, you can monitor inventory levels, identify dead zones, and analyze storage patterns. The software typically includes visualization tools that create heat maps showing which areas are underutilized and which are overcrowded, allowing you to redistribute items more effectively.
Many systems now incorporate AI and machine learning to predict seasonal storage needs and suggest optimal product placement based on picking frequency. This predictive capability helps you prepare for busy periods and maintain efficient space utilization year-round.
Popular features include barcode scanning, automated reordering systems, and 3D warehouse mapping. These tools work together to create a digital twin of your warehouse, making it easier to experiment with different layout options without physically moving items around.
For smaller operations, cloud-based inventory management solutions offer affordable alternatives to enterprise-level systems. These platforms can be accessed from any device, making it simple to manage your space even when you’re off-site.
The best part? Most modern systems integrate seamlessly with other warehouse management tools, creating a comprehensive solution that not only optimizes space but also improves overall operational efficiency.
Space-Saving Storage Equipment
Mobile Storage Solutions
Mobile storage solutions are game-changers when it comes to maximizing warehouse space efficiency. Rolling shelves and adjustable storage systems offer incredible flexibility, allowing you to create aisles only when needed and compress storage space when not in use. These dynamic systems can double or even triple your storage capacity compared to traditional fixed shelving.
Mobile shelving units operate on tracks installed in or on top of your existing floor, with wheels that enable smooth movement side-to-side. With a simple push or electronic control, you can access different sections of storage while keeping others compactly closed. This eliminates the need for multiple fixed aisles, reclaiming valuable floor space for other operations.
Adjustable storage solutions take flexibility even further. With modular components and adjustable shelving heights, you can quickly adapt your storage configuration to accommodate items of varying sizes. This versatility is particularly valuable when dealing with seasonal inventory changes or evolving storage needs.
Many modern mobile storage systems come equipped with safety features like motion sensors and automatic locks. Some even integrate with warehouse management software, allowing you to track inventory location and movement in real-time. For smaller operations, manual mobile systems offer a cost-effective alternative while still providing significant space-saving benefits.
When implementing mobile storage, consider factors like floor load capacity, aisle width requirements, and frequency of access to different items. This will help you choose the right system that balances space optimization with operational efficiency.
Modular Storage Options
One of the most effective ways to maximize warehouse space is through modular storage systems that adapt to changing needs. These versatile solutions allow you to reconfigure your storage layout quickly, making them perfect for evolving inventory requirements.
Consider implementing adjustable pallet racking systems that can be modified in height and width, accommodating different product sizes and quantities. Mobile shelving units on tracks can compress storage space by eliminating fixed aisles, potentially doubling your storage capacity. These systems slide together when not in access, creating a compact storage solution that opens only where needed.
Stackable storage bins and containers offer another layer of flexibility, allowing you to mix and match sizes while maintaining organization. Look for bins with interlocking features that ensure stability when stacked and can be easily labeled for inventory tracking.
For smaller items, modular drawer systems provide excellent organization while maximizing vertical space. These can be customized with different drawer sizes and dividers, perfect for storing tools, parts, or smaller inventory items.
Remember to choose systems that can grow with your business. Many modular solutions offer add-on components that let you expand your storage capacity without replacing existing units, making them a cost-effective long-term investment.
Optimizing warehouse space isn’t just about implementing a single solution – it’s about combining multiple strategies to create an efficient, productive environment. By adopting vertical storage solutions, implementing smart inventory management systems, and maintaining organized aisle layouts, you can dramatically improve your warehouse’s functionality.
Remember that success lies in the details: proper labeling, regular maintenance of storage systems, and ongoing staff training all play crucial roles in maintaining an optimized space. The integration of modern technology, from inventory tracking software to automated storage systems, can significantly enhance your optimization efforts while reducing human error and improving efficiency.
Start small by implementing one strategy at a time, measuring its impact, and then moving on to the next. Consider beginning with basic organization techniques before investing in more complex solutions. Even simple changes like reorganizing your most frequently accessed items or implementing a clear labeling system can yield impressive results.
Don’t forget to regularly review and adjust your optimization strategies as your needs evolve. What works today might need refinement tomorrow as your business grows or storage requirements change. By staying flexible and open to new solutions, you’ll create a warehouse space that not only meets your current needs but can adapt to future challenges.
Take the first step today – whether it’s conducting a space audit or researching automated storage solutions. Your warehouse’s potential for improved efficiency is waiting to be unlocked.